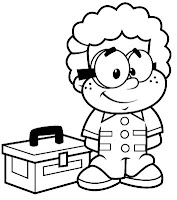
-Machinery’s Handbook
-Shigley’s Mechanical Engineering Design
-Making Things Move: DIY Mechanisms for Inventors, Hobbyists, and Artists (okay this one is a shameless plug, but Dug North told me it’s “destined to be be a classic of sorts” so you can blame him)
2. Project planning follows the rule of pi. Take how much time you think you can complete something in, multiply it by pi, and that will be the actual length of time it takes.
3. Parkinson’s Law: Work expands so as to fill the time available for its completion. Don’t give yourself too much time for a project or it will never get done. Speaking of done, check out The Cult of Done Manifesto. If it weren’t for the last minute, nothing would ever get done.
4. Everything is a spring.
5. If it moves and it shouldn’t, use duct tape. If it doesn’t move and it should, use WD-40.
6. Document everything you do. Someone will ask you to justify your design at some point, and “it kind of sort of looked right” is never a good answer. This is especially true on collaborative projects. The group will forget who did what and it will make going back and changing things that much harder.
7. Design is an iterative process. The necessary number of iterations is one more than the number you have currently done. This is true at any point in time.
8. Ask questions. If you don’t know something, say so. Your credibility as an engineer lies not in being infinitely intelligent, but in knowing how to get at the right resources to figure it out. If you cheat, people will die.
9. Designing for disassemble is just as important as design for assembly. It will never work the first time you put it together. Oh, and make sure that everywhere there is a screw, there is a place for a screwdriver to install it. And for a hand to fit around said screwdriver.
10. Business will always be a part of engineering. Don’t work for free (unless you really want to) and don’t work without a contract. Don’t design a better mousetrap THEN expect someone to want it. The products that sell the best are not necessarily the ones that are technologically superior.
11. Design is based on requirements. There’s no justification for designing something one bit “better” than the requirements dictate. Better is the enemy of good enough. Get it done then go play outside.
12. Engineering is done with numbers. Analysis without numbers is only an opinion.
13. Be friendly and talk to your machinist and/or shop techs. You may have a fancier title or degree, but that does not make you better. A short conversation on how to make a part more easily machinable/moldable/etc. can save thousands of dollars and make you both look good. You may even learn something.
_________________________________________
Original text is on this address: http://blog.makezine.com/archive/2011/03/the-beginning-mechanical-engineers-checklist.html
Ivan,
ReplyDeleteThe rule of Pi, is the most impressive. I faced this problem of Time over-runs at the begging of my carrier. I overcame this by simply increasing the estimated completion period by 3 times.
V V Ramana Rao